Have you ever faced the frustration of finding the perfect packaging solution, only to realize it doesn’t meet your needs? Maybe it lacks durability, isn’t eco-friendly, or simply doesn’t align with your brand identity. For industries ranging from logistics to cosmetics, packaging can make or break the safety, presentation, and transportability of your products.
But don’t worry—there’s a solution! Custom cardboard paper tubes are revolutionizing the packaging industry. They’re versatile, durable, and environmentally conscious, offering tailored options to suit your specific requirements. Stick with me, and I’ll share everything you need to know to make the best choice for your business.
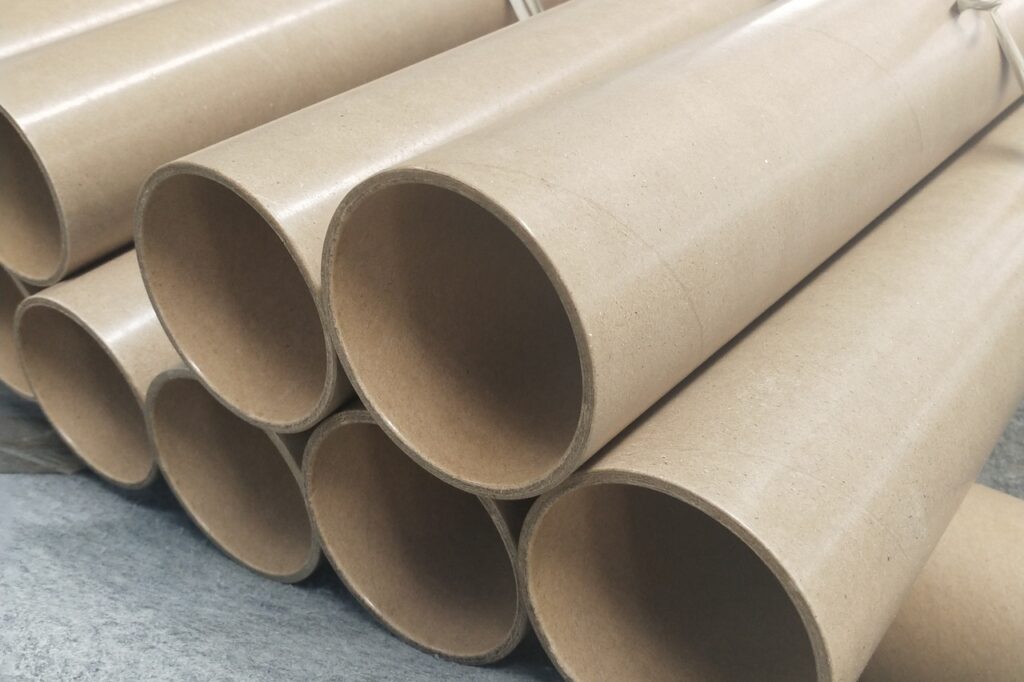
What Are Custom Cardboard Paper Tubes?
Custom cardboard paper tubes are cylindrical packaging solutions made primarily from recycled paper materials. They are not just sustainable but also highly customizable, making them suitable for various applications, from packaging fragile items to industrial uses.
Whether you’re shipping sensitive documents, packaging food products, or designing creative displays, understanding the structure, manufacturing process, and customization options is key to leveraging their full potential.
Manufacturing Process
The production of cardboard paper tubes involves several precise steps:
Material Selection: Typically made from kraft paper, fiberboard, or paperboard, many manufacturers prioritize recycled paper for sustainability.
Layering Technique: Paper strips are laminated and wound around a mandrel, with strength increasing as layers are added.
Custom Features: Functional and decorative elements, like aluminum linings or printed exteriors, can be included during production.
Key Features
Thickness & Strength: Thickness varies depending on ply count (from 3 to 30 layers), making tubes adaptable for light or heavy-duty use.
Surface Finishes: Options include colored or textured paper for aesthetic purposes.
Functional Additions: Handles, ribbons, or protective inserts enhance usability.
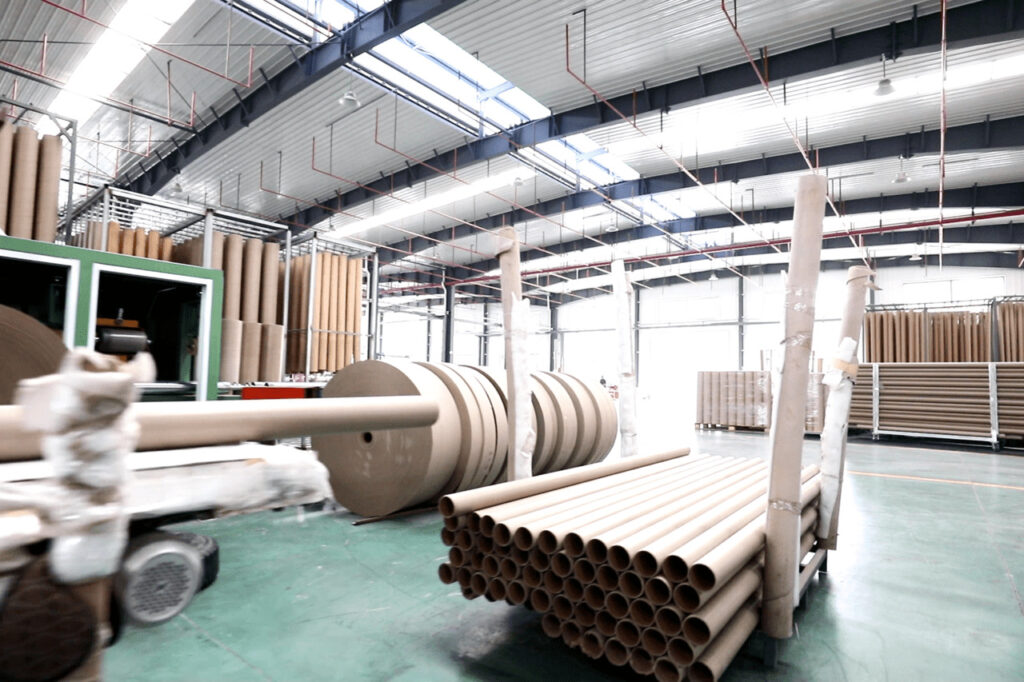
What Are the Different Types of Cardboard Tubes?
Custom cardboard tubes come in many types, each tailored to specific applications:
1. Spiral Wound Tubes
Made by wrapping paper at an angle, these tubes are highly durable and resistant to crushing. Ideal for packaging cosmetics and artwork.
2. Convolute Wound Tubes
Constructed with layers wound perpendicularly, offering exceptional dynamic strength. Common in construction and heavy-duty packaging.
3. Kraft Tubes
Lightweight yet sturdy, these tubes are perfect for mailing posters, documents, or artwork.
4. Shipping Tubes
Designed with added shock resistance to safely transport goods like artwork or fragile items.
5. Construction Tubes
Large, heavy-duty tubes used as molds for concrete pillars in construction.
6. Caulking Tubes
Used for dispensing caulk or adhesives in construction projects.
7. Paper Cores
Thick-walled tubes that provide structural support for materials like films, textiles, and wires.
8. Telescopic Tubes
Adjustable in length, these tubes offer flexible packaging solutions.
9. Paper Cans
Often used in food and cosmetics industries for their stylish appeal.
10. Custom-Shaped Tubes
Non-cylindrical options for unique packaging needs.
Each type serves a unique purpose, ensuring that businesses can find a solution tailored to their operational demands.
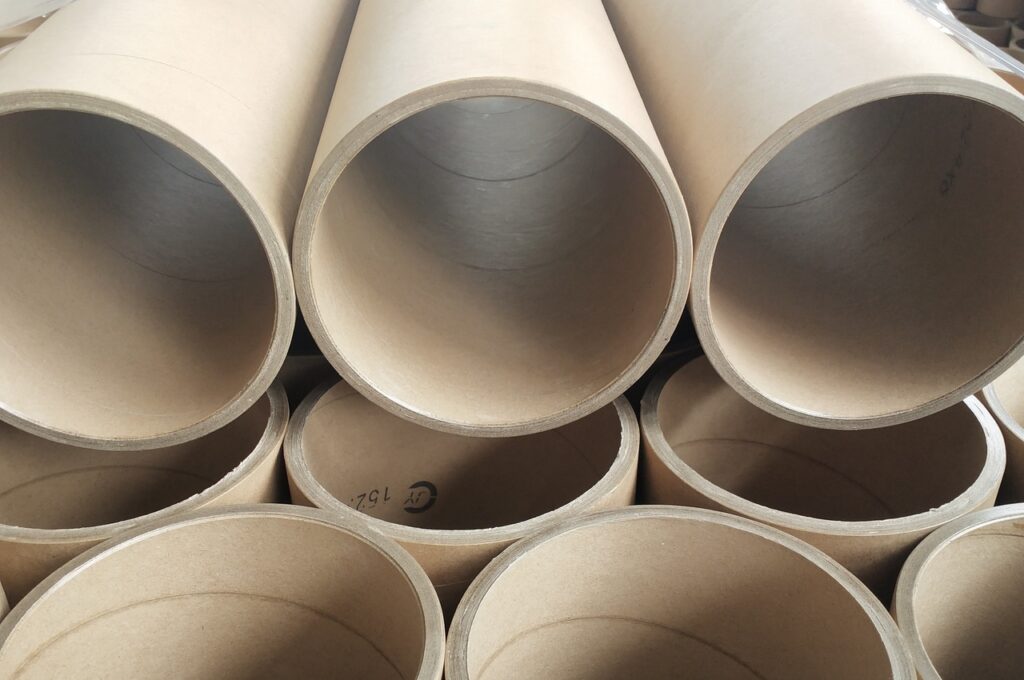
How to Make a Sturdy Cardboard Tube?
Creating a durable cardboard tube is both a science and an art. Here’s a step-by-step guide:
1. Material Selection
Kraft Paper: Use high-quality kraft paper for strength and durability.
Adhesives: Choose strong adhesives, like water-based PVA glue, for secure bonding.
2. Preparing the Paper
Cut kraft paper into strips, ensuring uniform width for consistent tube thickness.
Inspect for defects to maintain quality.
3. Applying Adhesive
Evenly coat paper strips with adhesive. Proper application is critical for ensuring strong bonds between layers.
4. Winding the Paper
Wrap the adhesive-coated strips around a mandrel using spiral or convolute techniques.
For extra durability, add multiple layers.
5. Curing and Drying
Allow the tube to cure and dry completely, using heat if necessary for faster and stronger adhesion.
6. Cutting to Length
Use a rotary cutter or saw to achieve precise, uniform cuts.
7. Finishing Touches
Add caps, waterproof coatings, or branding elements as needed.
Perform quality checks, including compression tests, to ensure durability.
By following these steps, you can create robust cardboard tubes for even the most demanding applications.
Custom cardboard tubes are more than just packaging; they’re an investment in sustainability, branding, and operational efficiency. The more you know about their types and manufacturing processes, the better equipped you’ll be to make informed decisions.
Next, let’s explore the deeper layers of customization: how to adapt these tubes for specific industries and what trends are shaping their use globally.
At Jinyin, we’ve spent over two decades perfecting the art and science of cardboard paper tubes. From understanding the nuances of material selection to offering tailored solutions for industries worldwide, our mission is to help you find the perfect packaging solution.
Whether you’re in logistics, construction, or consumer goods, custom cardboard tubes can elevate your operations. Let us know how we can help you design packaging that’s sustainable, cost-effective, and perfectly suited to your needs.
Contact us today for a consultation or sample request. Together, let’s build better packaging solutions!
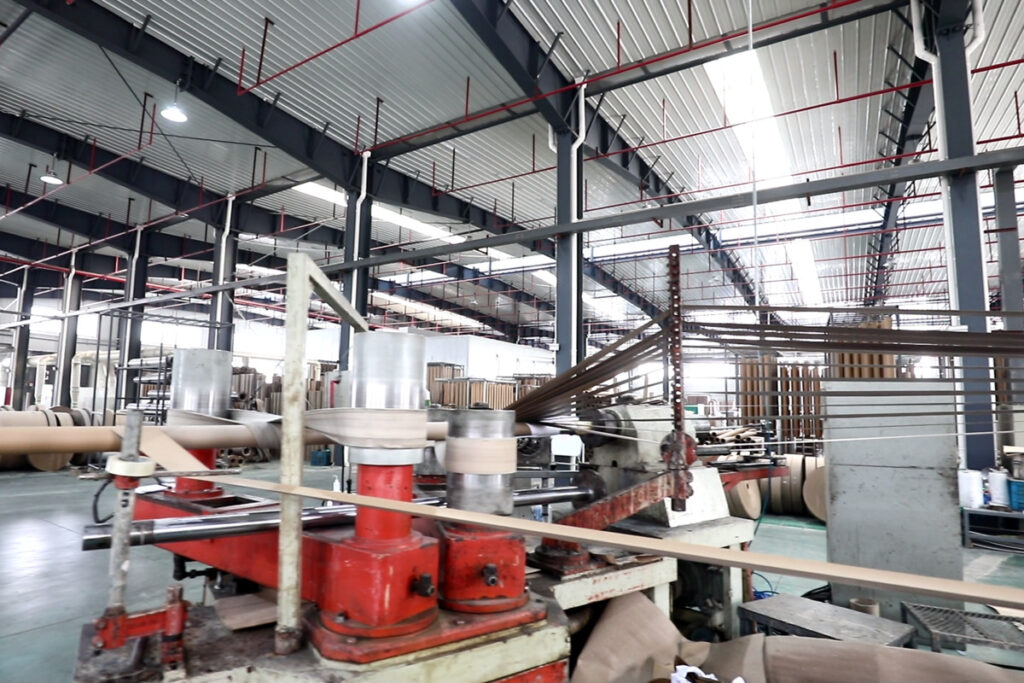